What makes a business a true industry leader?
In the area of sustainability, many people are doing great things to enhance the way that we, as individuals and corporations, interact with our environment. In recent decades, we have been blessed with incredible growth in technology. We have also been “cursed” a little by that growth. Now we have a huge responsibility … to conduct our business sustainably.
Unfortunately, we are missing the mark on living up to that responsibility.
Many organizations in today’s global market are dedicated to doing one thing: offering a good or service for which they have expertise in creating. In many of those companies, there is a department or team dedicated to sustainable business practices. That’s a nice idea, but is it enough?
It is rare to find a company whose core purpose includes reforming an industry in desperate need of greater sustainability.
That is precisely what Zip Xpress is doing in the supply-chain industry.
Zip Xpress and its allied company called Green Transportation Inc. were created because its owners saw a need in an industry that was — and still is! — stuck in its ways. And those “ways” of doing business? They’re not only unsustainable, down the road, they’re ultimately hazardous to social and economic well-being.
We all rely on trucking to keep our lives on track. Realize it or not, admit it or not; it’s a fact.
We need our “stuff” every day, and the supply chain that leads to our tables and cupboards and stores always has a truck in the picture, front and center. Problem is, the shipping industry has a massive problem: We are shipping huge amounts of dead air in our semi-trailers. Constantly, inefficiently, and arrogantly.
Big promises and corporate vows of “top-down, total organizational sustainability”? Hogwash, we say at Zip Xpress.
Virtually every manufacturer’s shipping department knows their company is blowing hot air with their sustainability claims when the truth of the matter is this: Companies wash their hands of efficiency and sustainability the minute their product is tossed into a truck that’s paid for by some unsuspecting customer. That customer could be paying $8,000 or more for a “full” load — even though the “fullness” is just a big load of dead air plus their couple of skids of product!
Do the Math; It’s Sobering
Shipping half-empty trailers — or worse — is “business as usual” for thousands of North American companies.
“Nothin’ but net” may be a good thing if you’re shooting hoops, but nothing but air is a crying shame.
Whoever’s paying the bill, it costs several thousand dollars or more to move a trailer, full or not. And if it’s not, well, it’s not sustainable for any of us. When a manufacturer or logistics firm allows a shipment of 11 pallets as a “full truck load” when the trailer can easily hold 28 pallets … everyone pays the price, sooner or later.
This massive misuse of time, talent, and trailers feeds into the North American driver shortages and inflicts unnecessary levels of wear and tear on the infrastructure. Zip Xpress, every day, tackles the issue and reduces wasteful business practices. Our system earns employees higher wages, reduces costs, makes products more affordable for everyone, increases the number of goods that can be sold, creates jobs – instead of adding to driver shortages – reduces expressway wear and tear, and improves highway safety. Zip’s model (in 2015 alone) saved an estimated 79,858 gallons of fuel, 659,626 miles of efficiency, and 1,941,013 pounds of CO, when compared with standard industry practices for Zip’s volume of business.
Interestingly, what we do is relatively simple (yet complex behind the scenes): We refuse to ship under-optimized trailers whenever humanly possible.
We don’t want our customers paying to ship dead air.
The Zip Xpress sustainability model makes us not only a more efficient company, we believe it will eventually lead to an entire industry becoming more sustainable.
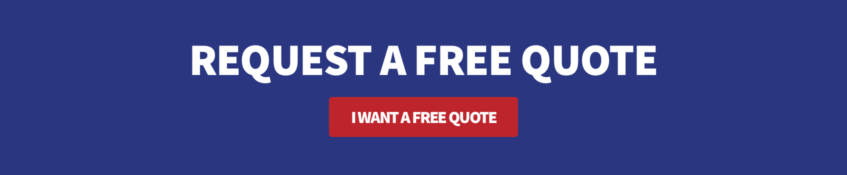