Whether your company owns your warehouse or you rent space from a third party, it is expensive and wasteful to have product sitting on the shelves for any excessive period of time. Inventory planning is an essential role in every organization’s supply chain, and should be taken seriously and evaluated regularly. The key to maximizing efficiency and maintaining a lean supply chain is to have just enough inventory ready to be shipped without running into shortages. This, of course, is easier said than done, but there are several ways manufacturers can make it happen.
Keeping track of previous trends and future projections is one of the biggest factors in planning your inventory. If you’ve maintained a steady level of growth over the past year, you’ll likely need to plan for higher stock levels in order to meet demand. With this comes your minimum inventory calculation. You want to be sure that you have enough stock to meet a customer’s demands in case of a spike in orders, but you don’t want to go overboard and have inventory sitting in a warehouse and costing money. So, this requires a safety stock level that will allow you to fulfill orders if you encounter an unexpected increase. Unfortunately, that will cost money in storage, but the key is to calculate how much money you would lose if you couldn’t fulfill customer orders and hedge against that. Even with storage fees, you’ll be more profitable if you are able to meet expectations.
At Zip Xpress, we understand the importance of being able to move inventory consistently. Our dedicated and experienced team can help you manage your inventory and adapt with your shipping timelines. We’ll create a customized carrier solution that suits the needs of your business, so you don’t have to rely on the ad hoc market. To see how we can keep your product moving, start today with Zip Xpress!
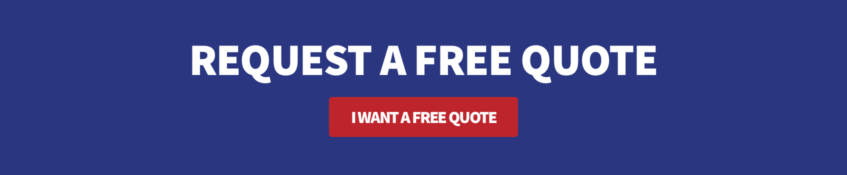